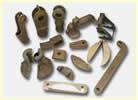
Sand Casting
Sand Casting The sand used for sand molding is critical and determines the favorable or unfavorable out come of the casting, it controls the tolerances, surface finish and the repeatability while in production. The sand must exhibit the following characteristics: Characters of sand casting:...
Sand Casting
The sand used for sand molding is critical and determines the favorable or unfavorable out come of the casting, it controls the tolerances, surface finish and the repeatability while in production. The sand must exhibit the following characteristics:
Characters of sand casting:
FLOWABILITY: The ability to pack tightly around the pattern.
PLASTIC DEFORMATION: Have the ability to deform slightly with out cracking so that the pattern can be withdrawn.
GREEN STRENGTH: Have the ability to support its own weight when stripped from the pattern, and also withstand pressure of molten metal when the mold is cast
PERMEABILITY: This allows the gases and seam to escape from the mold during casing.
All of these requirements are dependent on the amount of active clay present and on the water content of the mixture.
SAND CASTING BENEFITS
Least expensive casting process
Casting can be up to several tons
Less expensive than machining shapes from bar stock
Can cast intricate shapes
Can be used with most pourable metals and alloys
Green Sand Casting 01
Green sand-mold casting involves mixing sand with a suitable clay binder (usually a bentonite clay) and other additives, and packing the sand mixture tightly around a pattern that is constructed from the part design, but the pattern is not an exact replica of the part since various dimensional allowances must be made to accommodate certain physical effects. After extracting the pattern from the sand mold, a cavity is left behind that corresponds to the shape of the pattern. Next, molten metal is poured into this cavity and solidifies into a cast replica of the desired part. After the casting cools, the sand is readily removed from the casting and may be reclaimed for further use.
Green Sand Casting 02
The green sand moulding process requires sand, clay and water to be mixed together to form a mould material that can be compacted around a pattern to produce a mould. Water develops the bonding characteristics of the clay, which binds the sand together, when used in its moist condition it is referred to as green. The green sand process can be used to produce castings in both iron ,aluminium as well as copper based metals. The process allows 90% to 95% reclamation of material and so provides a low cost form of production.
Various high quality castings are made of gray iron, ductile iron, aluminum, steel, brass etc. Quality control checks are performed throughout the casting process form screening the raw material for stability the concentration of alloy and melted by the electric furnace. We analyze the chemical elements concentration of the alloy with spark spectrometer testing before casting¡£After casting and heat treatment we continue testing by metallurgical microstructure analysis, as well as checking tensile, impact strength and surface hardness by physical test and magnetic particle etc.
Resin sand Casting 01
resin-coated sand is packed tightly around a pattern. The pattern is removed, and the molten metal is poured into the corresponding cavity. The sand casting process is one of the most affordable methods of creating a metal casting.
Various high quality castings are made of gray iron, ductile iron, aluminum, steel, brass etc. Quality control checks are performed throughout the casting process form screening the raw material for stability the concentration of alloy and melted by the electric furnace. We analyze the chemical elements concentration of the alloy with spark spectrometer testing before casting¡£After casting and heat treatment we continue testing by metallurgical microstructure analysis, as well as checking tensile, impact strength and surface hardness by physical test and magnetic particle etc.
Shell Mold Casting
Benefits of Shell Mold Casting:
1. Shell molding process offers better surface finish.
2 Shell molding process offers better dimensional tolerances
3 Shell Molding Process offers higher throughput due to reduced cycle times.
A heated metal pattern is covered with a mixture of sand and thermoset plastic. This causes a skin of sand mixture to adhere to the pattern. This skin is removed from the pattern to form the "shell mold". The two halves of the shell mold are secured together and the metal is poured in the shell to form the part. Once the metal solidifies, the shell is broken.
The materials that can be used with this process are cast irons, and aluminum and copper alloys. Typical parts made with this process are connecting rods, gear housings, lever arms etc.
· The basic process for these molds is,
1. Create two mating patterns of desired shape.
2. Coat the molds with a shell (sand and binders, such as a resin) until desired thickness and other properties are obtained.
3. Cure the molds and remove the patterns.
4. The mold halves are mated and held firm while metal is poured.
5. The final part(s) is removed.
This technique can be very economical.
· Special care must be taken to assure venting for gasses, as the mold media is less porous. · This method can easily use cores and chills to make complex molds.
· Graphite molds can be used for materials that would normally react with other materials used for the molds
Shell molding process offers better surface finish, better dimensional tolerances, and higher throughput due to reduced cycle times.
A fairly high capital investment is required, but high production rates can be achieved. The process overall is quite cost effective due to reduced machining and cleanup costs.
The materials that can be used with this process are cast irons, and aluminum and copper alloys. Typical parts made with this process are connecting rods, gear housings, lever arms etc.
Resin sand Casting 02
Resin-coated sand is packed tightly around a pattern. The pattern is removed, and the molten metal is poured into the corresponding cavity. The sand casting process is one of the most affordable methods of creating a metal casting.
Various high quality castings are made of gray iron, ductile iron, aluminum, steel, brass etc. Quality control checks are performed throughout the casting process form screening the raw material for stability the concentration of alloy and melted by the electric furnace. We analyze the chemical elements concentration of the alloy with spark spectrometer testing before casting¡£After casting and heat treatment we continue testing by metallurgical microstructure analysis, as well as checking tensile, impact strength and surface hardness by physical test and magnetic particle etc.
Resin sand Casting 03
Resin-coated sand is packed tightly around a pattern. The pattern is removed, and the molten metal is poured into the corresponding cavity. The sand casting process is one of the most affordable methods of creating a metal casting.
Various high quality castings are made of gray iron, ductile iron, aluminum, steel, brass etc. Quality control checks are performed throughout the casting process form screening the raw material for stability the concentration of alloy and melted by the electric furnace. We analyze the chemical elements concentration of the alloy with spark spectrometer testing before casting¡£After casting and heat treatment we continue testing by metallurgical microstructure analysis, as well as checking tensile, impact strength and surface hardness by physical test and magnetic particle etc.
Iron Sand Casting
Iron Casting are a family of ferrous metals with a wide range of properties produced by being cast into shape as opposed by being formed,other elements are used to control specific properties, cast irons have a wide range of mechanical properties which make them suitable for use in engineering components. The wide spread use of cast iron is as a result of its low cost and versatile properties.
Most of material use are grey iron and ductile iron, which products weight are from less than 1kgs to several tons.
Advantages of Iron Casting:
Ductile Iron Casting provides Higher Tensile Strength.
Less Deflection Under Load Conditions.
No Straightening Required in Most Instances.
No Problems With Hot Tears and Cracks.
Good Machinability.
Easier Feeding of Difficult Designs.
Copper Sand Casting
Copper casting can be used to produce parts in shapes that cannot be easily attained with fabrication techniques, such as - forming or machining. The composition of copper casting alloys may differ from those of their wrought counterparts for a variety of reasons.
Usually casting allows greater latitude in the application of alloying elements, because the effects of composition on cold or hot working properties are not significant.
Most of the copper-base casting alloys that contain tin, lead or zinc have moderate tensile and yield strengths, low to medium hardness, and high elongation. In applications that require high tensile or yield strength, the aluminum bronzes, silicon brasses, manganese bronzes, silicon bronzes and some nickel silvers are used instead. Most of the high strength alloys have good resistance to corrosion and wear.
The properties of castings depend on the size of section and the process of casting.